Analysis of the effect of probe structure on sampling accuracy in supersonic airflow
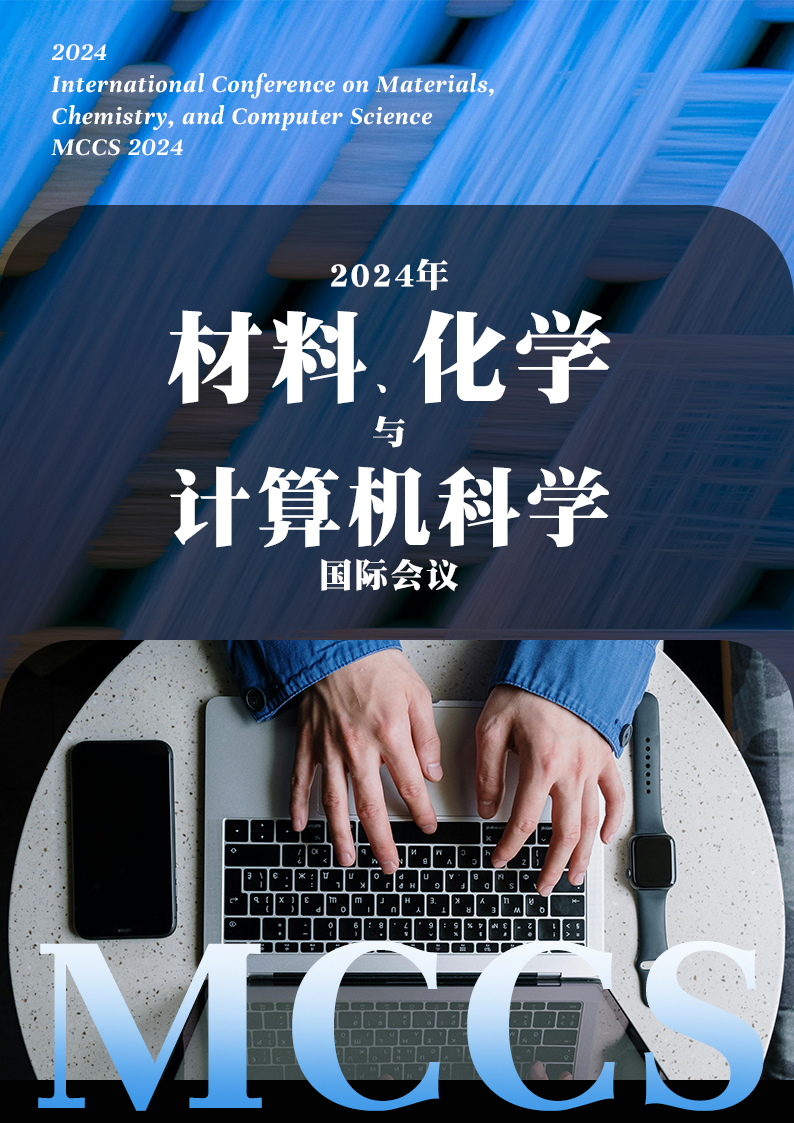
Authors:
Yingtao Chen, Wanlin Zhang, Pengpeng Sha, Xinlong Yang
Keywords:
supersonic airflow; sampling probe; sampling accuracy; numerical simulation.
Doi:
https://doi.org/10.70114/acmsr.2024.1.1.P32
Abstract
The accuracy of the sampling of the gas components has a significant impact on the measurement of various performance parameters in the combustion chamber of an aero-engine. This paper examines the accuracy of a six-point gas sampling probe when used in supersonic airflow. A numerical simulation method of component transport and fluid-solid coupling is employed to construct a three-dimensional probe multi-component gas flow characteristic solution model. Three kinds of probes with 28°, 30° and 32° angles and structure-modified conical probes were established, and the influence law of probe structure on gas sampling accuracy was analyzed. The results of the study demonstrate that the 28° and structurally modified conical probes yield a more effective improvement in sampling accuracy in comparison to the original 30° structure. The test data of the test bench are in good agreement with the simulation results, thereby demonstrating the reliability and accuracy of the sampling probe following structural modification.